Table of Content
This shows the finished product, the wheel, as well as another disc I made, and a video of just how surprisingly bouncy homemade plastic is. It's got a lot of visual texture/color swirls, but it's actually a pretty regular surface. The circle turned out very well, and you can carve on this, machine it, turn it, and drill it, if you want something more precise.
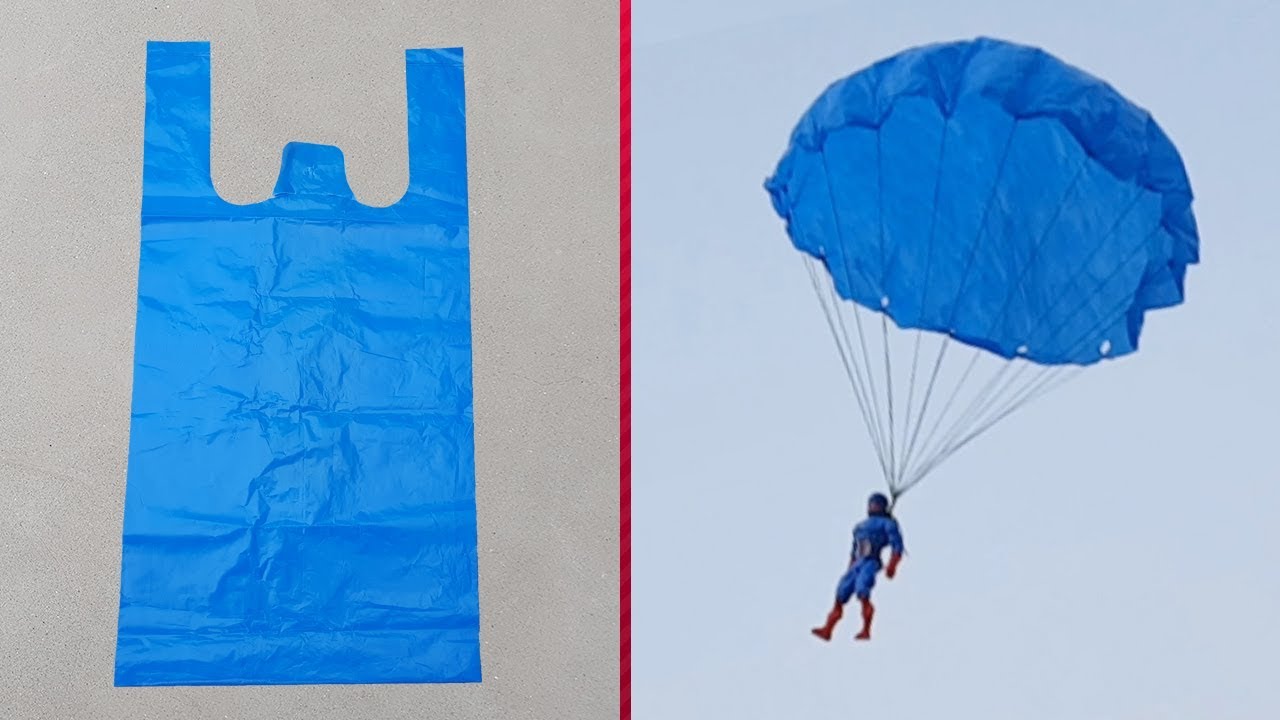
The cloth will appear white where is has not been thoroughly saturated. Fully wetting the cloth is where the strength of reinforced plastic comes from. I done tried this and it actually works a lot better if you don't shred the bags, because the more shredded it is the harder it is to mash and the worse it looks. I stuffed all the bags inside one bag and it came out with much fewer wrinkles, it was less oily and was easier to work with. Since I'm just experimenting, I grabbed a salsa container that looked about the right shape for a wheel mold, and a wine bottle to make the hole in the middle. If you wanted a smooth, non-oily finished surface, consider using wax instead.
how to make plastic pellets at home
If you fill each half with the liquid plastic and then put the halves together, you can make a copy of that object. You can also use a cookie cutter to cut shapes out of the plastic while it is still warm.An alternative to making your own mold, is to purchase a mold at a craft or hobby shop. Combine all of the ingredients in the saucepan and stir until there are no clumps left. You may need to use a whisk to disperse all of the clumps. Place the saucepan on the stove and start heating the mixture on medium-high heat.If you want to color your plastic, you can add a few drops of food coloring at this step. The main and auxiliary machines are integrated, the installation is simple, the footprint is small, and the performance and price ratio are outstanding.
At its peak, the machine can produce up to 4 parts per minute. The Model 150A also has a small chamber in which you can put your plastic pellets or tiny cut-up pieces of plastic soda bottles. A temperature controller allows you to set the temperature that you want your molten plastic mixture to be. The molten plastic then gets injected into your mold cavity through the machines injector. Youll most often see thermoplastics in plastic pellet form for injection molding purposes.
Structures of plastic pellet making machine
However, if your sawdust has been stored in a moist environment or feels wet to the touch, spread it out on a flat surface in a dry room for 24 hours to dry the dust. What you should see is an almost mirror image of your item formed into the epoxy mold which would now be formed on the second frame. The first frame will already have the hardened epoxy in it. Now place the second frame onto the first one and align it correctly.

"This email helped me a lot on how to make wood pellets, quite useful. Thank you very much." If you’re making the pellets for your own personal use, you can leave misshapen pellets in with the regular ones to avoid producing waste. This step isn’t necessary for small batches of pellets since they won’t be placed in an industrial mill. This step isn’t necessary if you’re starting with sawdust, since it’s already milled and refined to small pieces. If you want to produce a lot of plastic things in your own facility, a machine like this is very much the way to go. Its not the first machine of its type weve seen, either!
Plastic pellet making machine | PP PE plastic extruder
Recently, we had an entrepreneurial client come to us with an idea for a plastic part. He had jury-rigged an innovative gutter cleaner from parts he bought at a local hardware store. But he needed to scale his production to make the product commercially viable. He came to our team at Rex Plastics to find out whether plastic injection molding was right for his design. A ZLSLG300B plastic pellets making machine is indispensable. A good plastic pelletizer is very important for the whole recycling, which influences the quality of the final plastic pellets.
If you’re making a large batch of pellets and there’s a chance that the wood particles might contain stone or metal, carefully pour the raw material into the sieve. The build relies on a pair of beefy 3hp motors to drive the screw-based injection system. These are responsible for feeding plastic pellets from a hopper and then melting them and filling the injection reservoir, before then forcing the hot plastic into the mold. Further stepper motors handle clamping the mold and then releasing it and ejecting the finished part. A Raspberry Pi handles the operation of the machine, and is configured with a custom Python program that is capable of proper cycle operation.
There are quite a few injection molding machines available online which are fit for a DIY or domestic work environment. Clean plastic raw materials need to be crushed by crusher to meet the processing standard of plastic pellets making machine. The old customers who bought our plastic recycling pellet machine have reported to us that there is a strange smell after the waste plastic granulator is granulated. After experiments and research on this problem, our factory has discovered the cause of the peculiar smell of the plastic granulator. Our company has rich production experience in plastic recycling. There are many different plastic materials on the market.
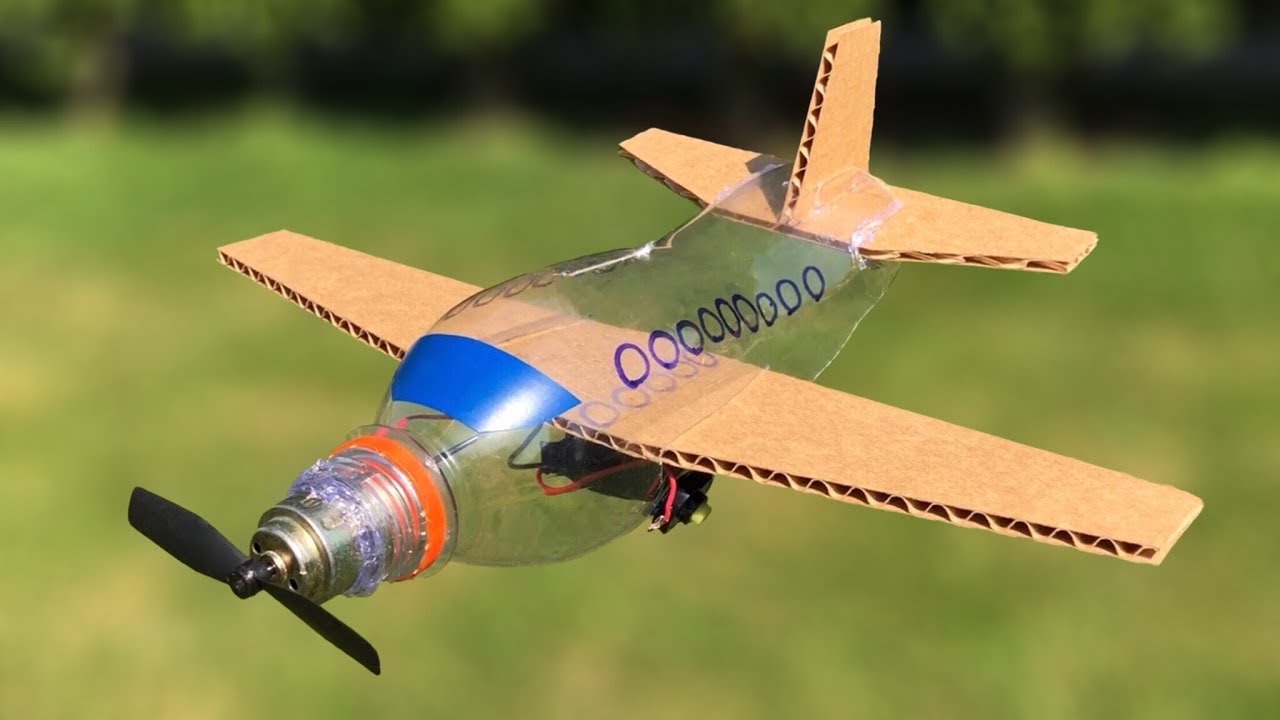
5.) Structures made out of the pellets can be painted with spray paint or with acrylic paint. Make sure that you are in a well-ventilated area when applying the paint. Reducers, die heads, and motors of Shuliy granulator machine are all the highest equipment currently on the market. A cutting device is installed at the bottom of the hopper to adjust and cut the material.
Chip the wood into pieces that are 2.5 cm (0.98 in) or smaller. Turn on the wood chipper by activating the ignition, and carefully feed the branches, logs, or other materials into the mouth of the chipper. Set a container at the opposite end of the chipper to catch the wood chips as they shoot out of the machine. Polyethylene is one of the most versatile plastics to use for injection molding. Polytheylenes high ductility, tensile strength, impact resistance, low moisture absorption, and recyclability make it an ideal material for plastic containers and bags.

3.) Plastic pellets can be placed into molds to produce special shapes. Molds are ideal if you want the pellets to take on a more delicate pattern or shape, and molds that are made out of flexible material like silicone are recommended for this purpose. If you will be using molds that are made out of stiffer material, you may want to apply a release agent at some point in the molding process. You can pass the pellets through an embossing machine once they are melted down and cooled into a sheet.